日本企業IHI開發出了一項低成本的航空引擎零部件加工技術。與傳統的鍛造法相比,該技術最多能削減80%的成本。為了讓飛機機身更輕,以提高燃油利用率,越來越多飛機製作商採用了特殊合金材料,生産加工成本也因此不斷提高。IHI希望通過提高成本競爭力來擴大零部件的銷售量。
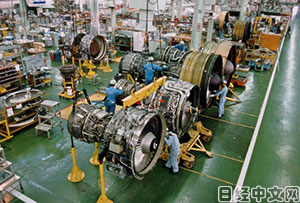 |
IHI的瑞穗航空引擎工廠 |
新技術的生産流程是將鈦和鎳等粉狀合金與樹脂混合,然後利用模具在攝氏150~450度的溫度下塑形;成型後將樹脂蒸發,並繼續加高溫讓金屬變堅固。以引擎為主的飛機和太空事業是IHI的最大收益源,佔其合併銷售額的約30%。公司計劃在2016年度之前將該技術投向實際使用。
現有技術通過鍛造、鑄造以及切削合金材料來加工成所需形狀。與此相比據稱新技術可以節省50~80%的生産成本。以該技術加工鈦和鎳等特殊合金材料在業界尚屬首次。
加工成本與3D列印相當,並且可以精密地加工出圓弧和角度等。IHI計劃把利用這項技術加工的小型風扇和壓縮機扇葉等合金零部件銷售給美國通用電氣(GE)和P&W等航空引擎生産商。
航空引擎的製造材料主要是重量輕且耐熱性較好的鈦和鎳。由於這些零部件對於引擎燃耗的改善起決定作用,因此在零部件廠商之間「品質提高」和「成本控制」競爭正變得日趨激烈。IHI將依靠新技術提高國際競爭力,不斷擴大産品在開發新型引擎過程中的採用率。
飛機的全球市場需求態勢良好。在這樣的背景下,IHI的引擎零部件生産數量自2011年以後就不斷更新著最高記錄。預計2016年時,全年可生産可供1800架飛機用零部件,與2011年相比産量將增長60%。美國波音公司預計將於2020年投入下一代大型飛機,而IHI也將參與大型飛機的引擎開發。
版權聲明:日本經濟新聞社版權所有,未經授權不得轉載或部分複製,違者必究。